Recycling of excessive amounts of biomass residue into boiler furnace is obscure and not well implied.
Palm oil mills are complete industrial installations within themselves, producing their own supply of steam and electricity by utilising waste materials generated during the oil extraction process. The steam is used for the sterilization of fresh fruit bunches (FFB) and oil clarification processes, whereas the electricity is used to power the mill.

The residue at the end of the oil and kernel extraction processes is pressed oil palm mesocarp fibre (MF) and palm kernel shell (PKS) comprising about 14 % and 6 % respectively of the FFB. These biomass materials are then recycled as boiler fuel for high-pressure steam generation. Traditionally, owing to the ready supply of large amounts of waste oil palm mesocarp fibre and palm kernel shell, right at their doorstep, mills have enjoyed the luxury of generating copious amounts of steam while disregarding its inefficient use along with the current state of inefficient operation of the process steam system, power plant and boilers. This generous and abundant steam supply has afforded a highly wasteful management of process steam.
The problem originates in the sterilisation process, mainly, because of the variances between its steam demand and the steam supply. The steam demands of sterilisation are irregular whereas the process steam supply from the power plant is regular. This results in cyclic steam blow-off and make-up, both being losses of energy. In addition, the present method of sterilisation is inefficient with regard to process steam use in terms of its required unnecessarily high steam pressure and consumption.
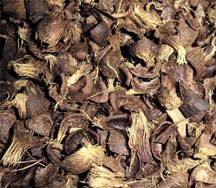
In reality, huge amounts of waste oil palm mesocarp fibre and palm kernel shell are being incinerated in boiler furnace in oil palm mills as a waste management strategy, in lieu of having them hauled away. Meanwhile, to-day, the value of the palm mesocarp fibre and palm kernel shell has appreciated greatly, because of its capacity to generate clean energy as a means to mitigate carbon emission in the production of palm oil, as well as in other industries.
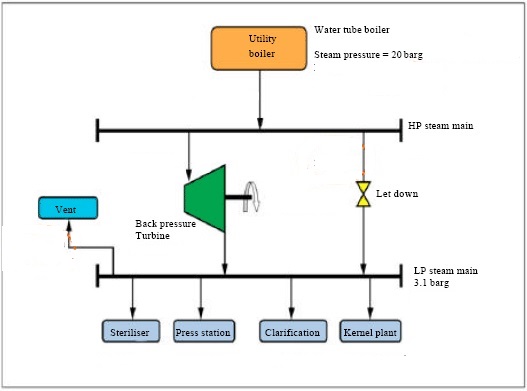
Presently, technologies are available for the improvement of energy efficiency (EE) in palm oil mills. The technologies exploit opportunities in resolving obscure discrepancies in the efficient use of energy at the mills in order to liberate and repurpose the waste oil palm mesocarp fibre and palm kernel shell for the purpose of additional electricity or Combined Heat and Power (CHP) generation.
The technologies accomplish the above by:
- Implementing a steam management system to reduce large steam losses due to the intermittent batch-wise steam needs of the mill for sterilization,
- Buffering the irregular steam demand from the batch-wise sterilisation to enable steady steam draw out from the boiler and thereby improving boiler operation efficiency to reduce the amount of oil palm mesocarp fibre and palm kernel shell required to generate steam and power the mill,
- Implementing an improved steam sterilisation system to reduce the steam needs of the mill for sterilization and improve electricity generation at the mill.
The combined effects of the technologies work synergistically to dramatically improve the energy efficiency of palm oil mill operations with the potential to liberate upwards of 50% of the waste biomass materials for electricity or CHP generation.
For instance, a palm oil mill of 60 tonnes/hour processing capacity could liberate more than 4 tonnes per hour of the surplus dry biomass material.
In addition, the technologies make the necessary technical provisions to realise the intrinsic potential efficiency for electricity generation in a scaled-up CHP plant at the mill. A 60 tonnes/hour capacity mill could generate up to 6 MW electricity using a fraction of the saved biomass. The remaining saved biomass could displace another 7.3 MW electricity via CHP elsewhere at load centres as local supplies (without using the problematic EFB).
While the recycling of needless amounts of the biomass residue into boiler furnace is ongoing unfazed, mesocarp fibre and palm kernel shell are extremely desirable as a renewable bio-fuel for the following reasons:
- As an agricultural waste, it is considered renewable biomass and energy generated from it would therefore be considered low-carbon renewable energy (RE);
- It has significant energy density and low moisture;
- It is low in potash, silica and other impurities which contribute to slagging in boilers;
- Ash content is minimal and non-toxic;
- Low bulk (compared to EFB); and
- Locally concentrated in Palm Oil Mills.
Additionally, harnessing this long-neglected energy source would:
- Increase both Palm Oil Plantation and Mill earnings;
- Green the image of the oil palm industry by reducing the carbon footprint (greenhouse gas emissions) of palm oil production;
- Further decrease the cost of electricity by combined heat and power generation as distributed generation for local supplies at load centres; and
- Moreover and more importantly, to avoid or reduce further climate change mainly due to CO2 emission, it was agreed (e.g. the Paris Agreement) that energy consumption and carbon emissions should significantly be reduced.
Imagine the economic wellbeing of the mill and the environmental wellbeing of the planet which could be unleashed!